Master 3.0
We confirm receipt of noncommittal demand
Demanded machine: Master 3.0
Company:
Kontaktní osoba:
VAT:
Adresa:
Phone:
E-mail:
Your inquiry:
Destination country:
We will contact you as soon as possible using given contact details.
Back to website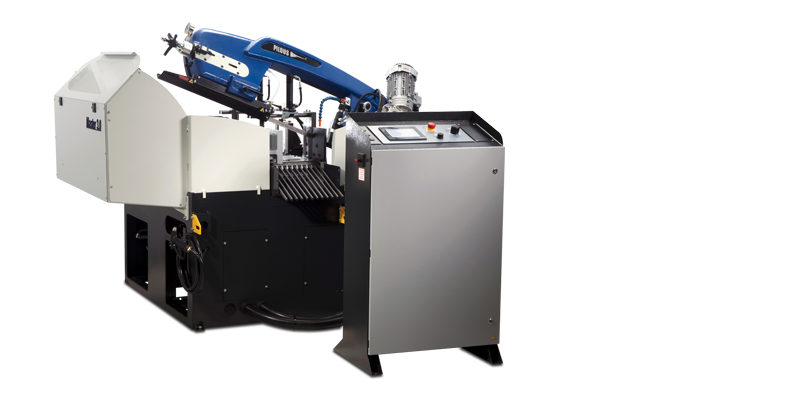
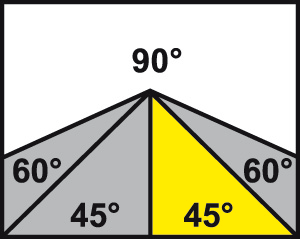
The new generation of Master series CNC automatic band saws represents the best in the market in terms of material cutting productivity in the engineering industry. Operator communication with the machine is simple and intuitive. The new software guides the operator step by step by entering all the necessary data, allowing efficient operation of the band saw within minutes of unpacking the machine.
Mechanically, the machine is designed with very small dimensions, while maintaining the same or better parameters to occupy the smallest possible footprint. Emphasis is placed on the rigidity of the entire machine. An extremely robust arm, hollow throughout its profile, cleverly conceals the hydraulic and electrical circuits. The CNC automatic machine is equipped with a material feeding mechanism using an industrial servomotor, which, together with a precise ball screw, ensures high speed and very accurate material feed even with multiple workpiece clamps. The feed speed can be set to three different values depending on the weight of the workpiece. The workpiece is placed on a continuous track, the feed is provided by rollers, thus avoiding abrasion of the workpiece. The machine can be connected to a workpiece bin. The workpiece is clamped by a feed vice and a main vice. It is also possible to fit a vice behind the cut for better workpiece clamping or a retractable hydraulic jaw on the feed vice for cutting crooked workpieces. Vertical clamping with HVP is now independently controlled and ensures comfortable clamping of workpiece bundles. The entire machine is controlled by a powerful industrial PLC computer. For comfortable operation, it is connected to a large 10" high-performance colour touch screen. The machine connection to the line or to a remote master control is handled by secure hardware.
You can program up to 49 different lengths and quantities of workpieces. Each such program can also be supplemented with a note or drawing number. In addition to the fully automatic mode, the machine can also be operated in manual mode. Workpiece clamping and arm feed with the saw blade is controlled by a hydraulic unit. The descent can be controlled by means of precision proportional hydraulic technology and an autonomous control system for increased comfort and cutting efficiency. The cutting tool is a 27x0.9mm saw blade, which is produced in many variants and enables industrial splitting of a wide range of materials, including stainless steel or tool steel. For maximum cutting productivity, you can set the optimum saw blade speed using a frequency converter in the range of 15–90 m/min for even greater cutting accuracy and increased saw blade service life.
Highlights of the brand new MASTER concept:
- Machine operating system developed by Pilous – DELTA Elite System
- Reduced minimum material residue (125 mm)
- Optimum saw blade cutting speed can be set via frequency converter in the range of 15–90 m/min, or up to 120 m/min as standard
- Retraction of the workpiece when the saw blade arm moves to the upper position, with the saw blade in constant motion. Extends the service life of carbide saw blades.
- Fully lifting clamping vices
- Independently controlled top clamps HVP
- Possibility to cut workpieces at an angle of 0–45°
- Pressure control in the main and feed vice for clamping different workpieces included as standard on the machine
- Retractable fixed jaw of the feed vice for crooked materials
- Automatic retraction and extension of the saw blade above the material according to the workpiece to reduce cutting times
- Roller track and very powerful servomotor for handling very heavy workpieces
- Rollers and replaceable jaws preventing damage to workpieces during handling, e.g. aluminium semi-products, etc.
- New robust design of the screw conveyor of chips with increased discharge capacity
- Sensors on the main vice along with the control system allow precise workpiece positioning without the need for end cutting
- Very simple and intuitive control system
- Information windows to assist the operator with software functions, error messages, etc.
- Advanced users can take advantage of an enormous amount of machine settings, user accounts, machine reports
- Managerial indicators of cutting productivity – cutting times, cutting productivity of operators, consumption of saw blades, etc.
- Diagnostic functions, maintenance checks, fluid changes, machine cleaning, etc.
- Machine status notifications by SMS or visually by a beacon
- Automatic control of feed pressure connected to precision proportional hydraulics
- Possibility to connect the machine to lines, remote control, control also by mobile phone
- Possibility of remote service support
- Possibility to increase machine security with optical fences and barriers, cameras
- Much more…
90° | +45° | |
![]() |
300 | 240 |
![]() |
285 | 220 |
![]() |
305 x 290 | 235 x 130 |
Main motor | 400 V, 50 Hz, 2,2 kW |
Pump motor | 400 V, 50 Hz, 0,05 kW |
Hydraulic motor unit | 400 V, 50 Hz, 0,55 kW |
Servo motor of the feed | 1,3 / 2 kW |
Feed rate of material | 1,6 / 2,5 / 3 m/min. |
Saw blade speed | 15-90 m/min. |
Working height of vice | 850 mm |
Hydraulic system oil | cca 26 l (ISO 6743/4-HM, DIN 51 524 part 2-HLP) |
Coolant tank | cca 35 l |
Machine dimensions | Dimension drawing |
Machine weight | 1020 kg |
-
Signalling beacon M3
Signalling beacon is designed for a remote check of the working status of the machine. Trichromatic beacon is fitted with LED lights of a high luminosity and visibility from all directions, thanks to a unique shape of lenses.
Green light – indication of a working mode of the machine, sawblade is in the cut. After cutting operation and sawblade stopping the light switches off signalling that a next cut can be started.
Red light – indication of malfunction, e.g. broken sawblade, main motor overload, opened safety cover and other failures leading to the stop of the machine.
Blue light - indication of material ending etc.
The sawblade replacement
-
The new generation of Master series CNC automatic band saws represents the best in the market in terms of material cutting productivity in the engineering industry. Operator communication with the machine is simple and intuitive. The new software guides the operator step by step by entering all the necessary data, allowing efficient operation of the band saw within minutes of unpacking the machine.
Mechanically, the machine is designed with very small dimensions, while maintaining the same or better parameters to occupy the smallest possible footprint. Emphasis is placed on the rigidity of the entire machine. An extremely robust arm, hollow throughout its profile, cleverly conceals the hydraulic and electrical circuits. The CNC automatic machine is equipped with a material feeding mechanism using an industrial servomotor, which, together with a precise ball screw, ensures high speed and very accurate material feed even with multiple workpiece clamps. The feed speed can be set to three different values depending on the weight of the workpiece. The workpiece is placed on a continuous track, the feed is provided by rollers, thus avoiding abrasion of the workpiece. The machine can be connected to a workpiece bin. The workpiece is clamped by a feed vice and a main vice. It is also possible to fit a vice behind the cut for better workpiece clamping or a retractable hydraulic jaw on the feed vice for cutting crooked workpieces. Vertical clamping with HVP is now independently controlled and ensures comfortable clamping of workpiece bundles. The entire machine is controlled by a powerful industrial PLC computer. For comfortable operation, it is connected to a large 10" high-performance colour touch screen. The machine connection to the line or to a remote master control is handled by secure hardware.
You can program up to 49 different lengths and quantities of workpieces. Each such program can also be supplemented with a note or drawing number. In addition to the fully automatic mode, the machine can also be operated in manual mode. Workpiece clamping and arm feed with the saw blade is controlled by a hydraulic unit. The descent can be controlled by means of precision proportional hydraulic technology and an autonomous control system for increased comfort and cutting efficiency. The cutting tool is a 27x0.9mm saw blade, which is produced in many variants and enables industrial splitting of a wide range of materials, including stainless steel or tool steel. For maximum cutting productivity, you can set the optimum saw blade speed using a frequency converter in the range of 15–90 m/min for even greater cutting accuracy and increased saw blade service life.
Highlights of the brand new MASTER concept:
- Machine operating system developed by Pilous – DELTA Elite System
- Reduced minimum material residue (125 mm)
- Optimum saw blade cutting speed can be set via frequency converter in the range of 15–90 m/min, or up to 120 m/min as standard
- Retraction of the workpiece when the saw blade arm moves to the upper position, with the saw blade in constant motion. Extends the service life of carbide saw blades.
- Fully lifting clamping vices
- Independently controlled top clamps HVP
- Possibility to cut workpieces at an angle of 0–45°
- Pressure control in the main and feed vice for clamping different workpieces included as standard on the machine
- Retractable fixed jaw of the feed vice for crooked materials
- Automatic retraction and extension of the saw blade above the material according to the workpiece to reduce cutting times
- Roller track and very powerful servomotor for handling very heavy workpieces
- Rollers and replaceable jaws preventing damage to workpieces during handling, e.g. aluminium semi-products, etc.
- New robust design of the screw conveyor of chips with increased discharge capacity
- Sensors on the main vice along with the control system allow precise workpiece positioning without the need for end cutting
- Very simple and intuitive control system
- Information windows to assist the operator with software functions, error messages, etc.
- Advanced users can take advantage of an enormous amount of machine settings, user accounts, machine reports
- Managerial indicators of cutting productivity – cutting times, cutting productivity of operators, consumption of saw blades, etc.
- Diagnostic functions, maintenance checks, fluid changes, machine cleaning, etc.
- Machine status notifications by SMS or visually by a beacon
- Automatic control of feed pressure connected to precision proportional hydraulics
- Possibility to connect the machine to lines, remote control, control also by mobile phone
- Possibility of remote service support
- Possibility to increase machine security with optical fences and barriers, cameras
- Much more…
-
90° +45° 300 240 285 220 305 x 290 235 x 130 Main motor 400 V, 50 Hz, 2,2 kW Pump motor 400 V, 50 Hz, 0,05 kW Hydraulic motor unit 400 V, 50 Hz, 0,55 kW Servo motor of the feed 1,3 / 2 kW Feed rate of material 1,6 / 2,5 / 3 m/min. Saw blade speed 15-90 m/min. Working height of vice 850 mm Hydraulic system oil cca 26 l (ISO 6743/4-HM, DIN 51 524 part 2-HLP) Coolant tank cca 35 l Machine dimensions Dimension drawing Machine weight 1020 kg -
-
Signalling beacon M3
Signalling beacon is designed for a remote check of the working status of the machine. Trichromatic beacon is fitted with LED lights of a high luminosity and visibility from all directions, thanks to a unique shape of lenses.
Green light – indication of a working mode of the machine, sawblade is in the cut. After cutting operation and sawblade stopping the light switches off signalling that a next cut can be started.
Red light – indication of malfunction, e.g. broken sawblade, main motor overload, opened safety cover and other failures leading to the stop of the machine.
Blue light - indication of material ending etc.
-
The sawblade replacement