ARG 640 DCT S.A.F.
We confirm receipt of noncommittal demand
Demanded machine: ARG 640 DCT S.A.F.
Company:
Kontaktní osoba:
VAT:
Adresa:
Phone:
E-mail:
Your inquiry:
Destination country:
We will contact you as soon as possible using given contact details.
Back to website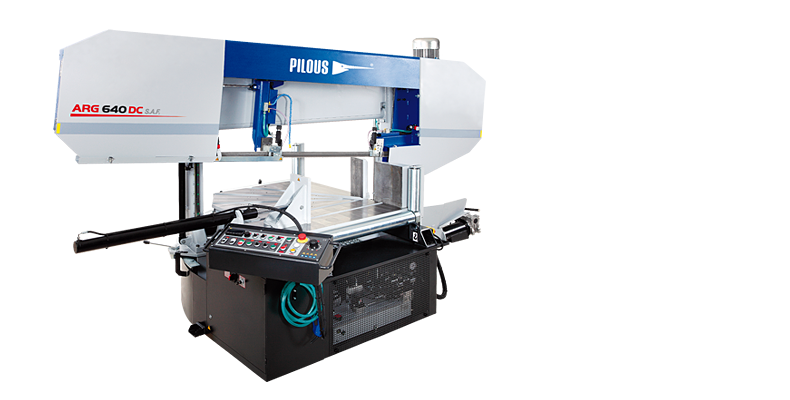
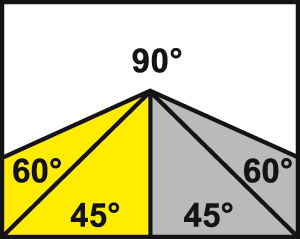
Powerful band saw with a massive dual-column support of the saw band arm which moves on linear guidance. That ensures excellent stiffness of the whole system and precise cutting. The modern conception of a massive band saw arm allows for industrial cutting of full materials of large sections, cutting of very large sections and also for cutting under 60°. The robust industrial band saw is generally suitable for all demanding production plants. The saw band sized 54 x 1.6 mm ensures accurate cutting of large cross-sections. The band is manufactured in many versions and allows for cutting of wide range of materials, including stainless steel or tool steel. Thanks to an exceptionally robust base, the system of rotary dual-column arm support and remarkably large loading surface of the vice the machine excels in its category. All of this ensures unique stability, accuracy and service life.
Easy intuitive controls throug an ergonomic rotary central panel. When you switch to the manual mode you can control all functions separately. The machine is equipped with a high-performance industrial hydraulic unit which allows setting of the contact pressure of the vice. All of this in connection with hydraulics-controlled saw band feed into cut significantly increases cutting efficiency, especially in larger series and cutting of full and high-quality materials. Both saw band guiding heads are fitted with automatic regulation of feed into cut, which significantly increases the rate and accuracy of cutting and service life of the saw band. Pressing a single switch will execute complete cutting cycle – material clamping, band and cooling system start, cutting, band and cooling stop, arm uplift to the original adjustable position and vice unclamping. Hydraulic unit allows you to set the required pressure of the vice. Maximum cutting efficiency is maintained also thanks to the possibility of setting optimum saw band rate by a frequency converter in the range between 15 and 90 m/min., which significantly contributes to cutting accuracy and service life of saw bands.
Plenty of accessories in the basic version:
- Double-sided automatic regulation of saw band feed into cut according to the resistance of the material to be cut.
- Hydraulic feed of saw band guide according to the cross-section of the material to be cut is controlled from the central panel.
- Hydraulic saw band tensioning controlled from the central panel ensures optimum tension and control of it during the operation of the machine. Optimum tensioning of the saw band is essential for its service life and cutting accuracy.
- Electrically driven cleaning brush for the saw band.
- Automatic removal of chips by a screw conveyor.
- Rinse spray gun.
- The system is mounted on tapered roller bearings in order to facilitate the easiest possible rotation of the arm during angular cutting.
- Simple locking and adjusting of a required cutting angle on the angle scale or, as additional accessories, digital monitoring on a touch screen.
- Massive full uplift vice ensures easy, quick and reliable material clamping.
- Large diameter running wheels and precise three-side hardmetal guiding ensure long service life of the band and cutting accuracy.
- Overdesign of running wheel bearings, tensioning wheel system and all rotary parts ensures long service life of the machine.
- Noiseless and maintenance-free band drive is provided by an industrial electric motor with bevel gearbox.
- The machine is connected to a complete cooling system with a pro-fessional pump and possibility of regulating the flow on both guiding heads independently, on an additional adjustable outlet and on a rinse spray gun. Coolant tank with a pump is placed in the base of the machine.
- The machine checks correct tension or break of the saw band. If the saw band breaks the machine automatically switches off.
- Easy control by ergonomically placed controls (electrical and hydraulics) on a rotary panel.
90° | -45° | -60° | |
![]() |
640 | 640 | 375 |
![]() |
550 | 550 | 375 |
![]() |
1100 x 550 | 710 x 550 | 375 x 550 |
Main motor | 400 V, 50 Hz, 7,5 kW |
Pump motor | 400 V, 50 Hz, 0,12 kW |
Hydraulic motor unit | 400 V, 50 Hz, 1,1 kW |
Saw blade speed | 15-90 m/min. |
Working height of vice | 800 mm |
Hydraulic system oil | cca 26 l (ISO 6743/4-HM, DIN 51 524 part 2-HLP) |
Coolant tank | cca 100 l |
Machine dimensions (min.) | 3800 x 2500 x 2050 mm |
Machine dimensions (max.) | 3800 x 2700 x 2700 mm |
Machine weight | 4200 kg |
-
Powerful band saw with a massive dual-column support of the saw band arm which moves on linear guidance. That ensures excellent stiffness of the whole system and precise cutting. The modern conception of a massive band saw arm allows for industrial cutting of full materials of large sections, cutting of very large sections and also for cutting under 60°. The robust industrial band saw is generally suitable for all demanding production plants. The saw band sized 54 x 1.6 mm ensures accurate cutting of large cross-sections. The band is manufactured in many versions and allows for cutting of wide range of materials, including stainless steel or tool steel. Thanks to an exceptionally robust base, the system of rotary dual-column arm support and remarkably large loading surface of the vice the machine excels in its category. All of this ensures unique stability, accuracy and service life.
Easy intuitive controls throug an ergonomic rotary central panel. When you switch to the manual mode you can control all functions separately. The machine is equipped with a high-performance industrial hydraulic unit which allows setting of the contact pressure of the vice. All of this in connection with hydraulics-controlled saw band feed into cut significantly increases cutting efficiency, especially in larger series and cutting of full and high-quality materials. Both saw band guiding heads are fitted with automatic regulation of feed into cut, which significantly increases the rate and accuracy of cutting and service life of the saw band. Pressing a single switch will execute complete cutting cycle – material clamping, band and cooling system start, cutting, band and cooling stop, arm uplift to the original adjustable position and vice unclamping. Hydraulic unit allows you to set the required pressure of the vice. Maximum cutting efficiency is maintained also thanks to the possibility of setting optimum saw band rate by a frequency converter in the range between 15 and 90 m/min., which significantly contributes to cutting accuracy and service life of saw bands.
Plenty of accessories in the basic version:
- Double-sided automatic regulation of saw band feed into cut according to the resistance of the material to be cut.
- Hydraulic feed of saw band guide according to the cross-section of the material to be cut is controlled from the central panel.
- Hydraulic saw band tensioning controlled from the central panel ensures optimum tension and control of it during the operation of the machine. Optimum tensioning of the saw band is essential for its service life and cutting accuracy.
- Electrically driven cleaning brush for the saw band.
- Automatic removal of chips by a screw conveyor.
- Rinse spray gun.
- The system is mounted on tapered roller bearings in order to facilitate the easiest possible rotation of the arm during angular cutting.
- Simple locking and adjusting of a required cutting angle on the angle scale or, as additional accessories, digital monitoring on a touch screen.
- Massive full uplift vice ensures easy, quick and reliable material clamping.
- Large diameter running wheels and precise three-side hardmetal guiding ensure long service life of the band and cutting accuracy.
- Overdesign of running wheel bearings, tensioning wheel system and all rotary parts ensures long service life of the machine.
- Noiseless and maintenance-free band drive is provided by an industrial electric motor with bevel gearbox.
- The machine is connected to a complete cooling system with a pro-fessional pump and possibility of regulating the flow on both guiding heads independently, on an additional adjustable outlet and on a rinse spray gun. Coolant tank with a pump is placed in the base of the machine.
- The machine checks correct tension or break of the saw band. If the saw band breaks the machine automatically switches off.
- Easy control by ergonomically placed controls (electrical and hydraulics) on a rotary panel.
-
90° -45° -60° 640 640 375 550 550 375 1100 x 550 710 x 550 375 x 550 Main motor 400 V, 50 Hz, 7,5 kW Pump motor 400 V, 50 Hz, 0,12 kW Hydraulic motor unit 400 V, 50 Hz, 1,1 kW Saw blade speed 15-90 m/min. Working height of vice 800 mm Hydraulic system oil cca 26 l (ISO 6743/4-HM, DIN 51 524 part 2-HLP) Coolant tank cca 100 l Machine dimensions (min.) 3800 x 2500 x 2050 mm Machine dimensions (max.) 3800 x 2700 x 2700 mm Machine weight 4200 kg -
-
-