Xpert 3.0 3D
Confirmamos la recepción de la consulta no vinculante
Máquina de interés: Xpert 3.0 3D
Empresa:
Kontaktní osoba:
IČO:
Adresa:
Teléfono:
E-mail:
Su pregunta:
Región de destino:
Tan pronto sea posible nos pondremos en contacto con los datos que ha ingresado.
Volver a la página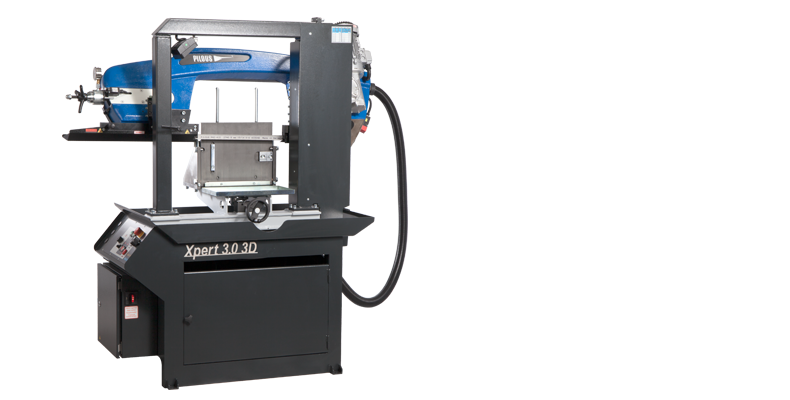
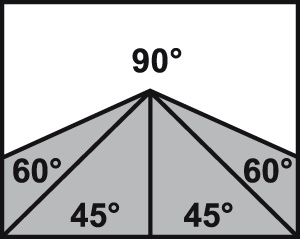
THE ARG 300 3D BAND SAW IS THE FASTEST, CHEAPEST AND MOST EFFECTIVE SOLUTION DESIGNED FOR THE DIVISION OF 3D PRINTED METAL PARTS FROM THE BASE PLATE.
This robust two-column band saw ensures fast and precise division of the 3D-printer-product from the printing plate. The cutting accuracy is 0.1 mm in all directions, the cutting width 1.5 mm.
Special adjustable printing plate clamping system ensures optimal fixation. It is equipped with a tipping mechanism with stops. This allows easy and fast clamping of the printing plate in the horizontal position and simple tipping to the vertical working position. Precise clamping of the printing plate ensures cut setting with minimum allowances, which saves material when printing. The distance between the cut and the base plate can be easily manually adjusted using the control wheel.
The maximum printing plate size is 300 x 300 mm. We will adjust the spacing and thread diameter according to your requirements.
The continuously adjustable jaw of the clamping system allows the installation of a 10–60mm thick printing plate with the possibility of mechanical adjustment up to a range of 0–70 mm.
In the standard design, the clamping system jaw can hold a 250x250mm base plate.
The plate can be clamped in two ways:
1. Using screws, standard thread spacing 210 x 210 mm. In the clamping system jaw, these threads are fitted with replaceable inserts, so you can choose the thread size according to the hole diameter for the screw in the printing plate, M5, M6 and M8. The insert can also be replaced if the thread is damaged.
2. Using the quick-clamping system - very easy clamping by tightening a single screw. The quick-clamping system can be adjusted to the size of the ptinting plate according to your requirements.
The machine is seated on an innovative base, which was designed with emphasis not only on sufficient stability, but also on minimum size (the base width is only 700 mm) and easy removal of chips from the machine tray into a removable container.
Lighting of cutting are is solved by LED lamp.
A completely new and revolutionary concept of the saw arm cast is designed in a unique way. The massive cast iron arm is entirely unrivalled in the category of dual-column band saws. It ensures, in the combination with the massive dual-column arm fit moving on linear lines excellent stiffness of the whole system and an accurate cut.
The cutting tool used is an industrial Bi-metal saw blade of the size 27 x 0.9 mm. Precision of the cut is guaranteed by a three-sided hardmetal guiding before and after the cut. Maximum cutting efficiency is maintained also thanks to the possibility of setting optimum saw band speed by a frequency converter in the range between 20-130 m/min., which significantly contributes to cutting accuracy and service life of the saw bands.
The saw blade arm moves on the linear guiding using hydraulic cylinder driven by a powerful hydraulic unit. It features simple operation on a central control panel and infinitely adjustable feed rate into the cut. After the execution of the cut, the saw blade automatically turns off and its arm moves up to the original, adjustable position.
The machine is characterized by its overall robust design. Its base consists of a stable machine pedestal with the printing plate clamping system the vice and a two-column fitting system of the arm that moves on linear guiding. The unique saw blade arm is fitted with orbital cast-iron wheels with massive fit, driven by an industrial engine with a worm gear. All this guarantees long-term cutting precision and service life of the machine.
All pictures shown are for illustration purpose only. Actual product may vary due to product enhancement.
Max. width and height of the printing plate | 300 x 300 mm |
Main motor | 400 V, 50 Hz, 2,2 kW |
Hydraulic unit motor | 400 V / 50 Hz / 0,18 kW |
Saw blade speed | 20-130 m/min. |
Operating vice height | 900 mm |
Oil in the hydraulic system | cca 6 l (ISO 6743/4-HM, DIN 51 524 part 2-HLP) |
Machine dimensions (max.) | 1900 x 980 x 1900 mm |
Machine weight | 513 kg |
-
Suction box
The suction box helps to exclude dust and chips from the cutting area. Suctioning is divided into two branches. The connection hole for powerful suction device has a diameter of 50 mm.
With a printing plate size of 250x250x20mm, the maximum printing height is 300mm
With a printing plate size of 300x300x20mm, the maximum printing height is 250mmThis accessory cannot be combined with the following accessories: Cooling of the saw blade and Cleaning brush
-
Cooling of the saw blade
Cooling of the saw blade prolongs the lifetime of the blade, removes chips, and contributes to a higher cut quality. The coolant pump starts up together with the saw blade. The amount of emulsion is dosed by a valve on the guiding heads. The emulsion is returned to the system through the waste container.
This accessory cannot be combined with the following accessories: Suction box
-
THE ARG 300 3D BAND SAW IS THE FASTEST, CHEAPEST AND MOST EFFECTIVE SOLUTION DESIGNED FOR THE DIVISION OF 3D PRINTED METAL PARTS FROM THE BASE PLATE.
This robust two-column band saw ensures fast and precise division of the 3D-printer-product from the printing plate. The cutting accuracy is 0.1 mm in all directions, the cutting width 1.5 mm.
Special adjustable printing plate clamping system ensures optimal fixation. It is equipped with a tipping mechanism with stops. This allows easy and fast clamping of the printing plate in the horizontal position and simple tipping to the vertical working position. Precise clamping of the printing plate ensures cut setting with minimum allowances, which saves material when printing. The distance between the cut and the base plate can be easily manually adjusted using the control wheel.
The maximum printing plate size is 300 x 300 mm. We will adjust the spacing and thread diameter according to your requirements.
The continuously adjustable jaw of the clamping system allows the installation of a 10–60mm thick printing plate with the possibility of mechanical adjustment up to a range of 0–70 mm.
In the standard design, the clamping system jaw can hold a 250x250mm base plate.
The plate can be clamped in two ways:
1. Using screws, standard thread spacing 210 x 210 mm. In the clamping system jaw, these threads are fitted with replaceable inserts, so you can choose the thread size according to the hole diameter for the screw in the printing plate, M5, M6 and M8. The insert can also be replaced if the thread is damaged.
2. Using the quick-clamping system - very easy clamping by tightening a single screw. The quick-clamping system can be adjusted to the size of the ptinting plate according to your requirements.
The machine is seated on an innovative base, which was designed with emphasis not only on sufficient stability, but also on minimum size (the base width is only 700 mm) and easy removal of chips from the machine tray into a removable container.
Lighting of cutting are is solved by LED lamp.
A completely new and revolutionary concept of the saw arm cast is designed in a unique way. The massive cast iron arm is entirely unrivalled in the category of dual-column band saws. It ensures, in the combination with the massive dual-column arm fit moving on linear lines excellent stiffness of the whole system and an accurate cut.
The cutting tool used is an industrial Bi-metal saw blade of the size 27 x 0.9 mm. Precision of the cut is guaranteed by a three-sided hardmetal guiding before and after the cut. Maximum cutting efficiency is maintained also thanks to the possibility of setting optimum saw band speed by a frequency converter in the range between 20-130 m/min., which significantly contributes to cutting accuracy and service life of the saw bands.
The saw blade arm moves on the linear guiding using hydraulic cylinder driven by a powerful hydraulic unit. It features simple operation on a central control panel and infinitely adjustable feed rate into the cut. After the execution of the cut, the saw blade automatically turns off and its arm moves up to the original, adjustable position.
The machine is characterized by its overall robust design. Its base consists of a stable machine pedestal with the printing plate clamping system the vice and a two-column fitting system of the arm that moves on linear guiding. The unique saw blade arm is fitted with orbital cast-iron wheels with massive fit, driven by an industrial engine with a worm gear. All this guarantees long-term cutting precision and service life of the machine.
All pictures shown are for illustration purpose only. Actual product may vary due to product enhancement.
-
Max. width and height of the printing plate 300 x 300 mm Main motor 400 V, 50 Hz, 2,2 kW Hydraulic unit motor 400 V / 50 Hz / 0,18 kW Saw blade speed 20-130 m/min. Operating vice height 900 mm Oil in the hydraulic system cca 6 l (ISO 6743/4-HM, DIN 51 524 part 2-HLP) Machine dimensions (max.) 1900 x 980 x 1900 mm Machine weight 513 kg -
-
Suction box
The suction box helps to exclude dust and chips from the cutting area. Suctioning is divided into two branches. The connection hole for powerful suction device has a diameter of 50 mm.
With a printing plate size of 250x250x20mm, the maximum printing height is 300mm
With a printing plate size of 300x300x20mm, the maximum printing height is 250mmThis accessory cannot be combined with the following accessories: Cooling of the saw blade and Cleaning brush
-
Cooling of the saw blade
Cooling of the saw blade prolongs the lifetime of the blade, removes chips, and contributes to a higher cut quality. The coolant pump starts up together with the saw blade. The amount of emulsion is dosed by a valve on the guiding heads. The emulsion is returned to the system through the waste container.
This accessory cannot be combined with the following accessories: Suction box
-